Sprayed polymer gypsum (MP Ultra)
MP ULTRA is a gypsum and polymer-based coating for spraying with gypsum spraying machine.
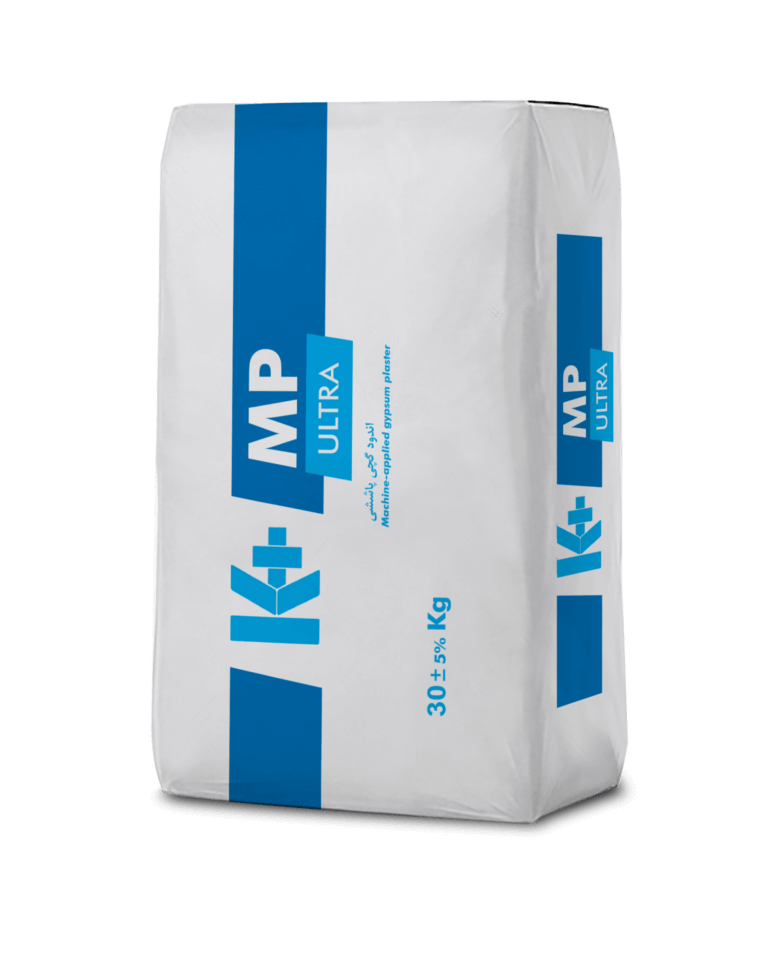
Properties and added value
■ For interiors
■ Mineral-based
■ Light and high yield
■ Establishes a comfortable and healthy room atmosphere
■ Regulates moisture and is diffusion permeable
■ Fire protection effective
■ Abrasion-resistant and nail-proof
■ Hand or machine application
Product description
Projection plaster MP ULTRA is light and particularly efficient premixed gypsum plaster based dry mortar with special light aggregates for smoothed interior surfaces.
Storage
Store the bags on wooden pallets in a dry environment. The product can be stored for 6 months. Seal damaged and opened bags airtight and use them up to 7 days.
Standards referred to
ISIRI 12015- 1 and EN 13279- 1 category B4/50/2, the product is subject to initial type testing and continuous factory production control.
Field of application
Plaster for creation of smoothed, freely-structured or levelled surfaces for interior walls and ceilings. As a single-layer plaster for all kinds of masonry, concrete as well as stable plasterable substrates.
■ From the cellar right up to the roof, suitable for all rooms with usual levels of room humidity including domestic kitchens and bathrooms (e.g. WCs in schools and bathrooms in hotels, hospitals, residential-care and nursing homes)
■ As a substrate for tiles, finishing plasters, coatings or wallpapers
■ For the provision of surfaces in quality levels
▪ Q1 to Q3 levelled
▪ Q1 to Q4 smoothed
▪ Q4 smoothed
Application
Clean the substrate of dust and loose parts and remove, ensure that the surface is smooth. All substrates must be stable, dry, even and free of grease and dust as well as free of any residual substances that may reduce the adhesion.
Cover easily-soiled building components before commencement in accordance. Preparation of the substrate in accordance with the table «Substrate and pretreatment». Ensure that the drying time for the preliminary / primer coats is observed before continuing work. Using the plaster base, correctly applied and/or pretreated concrete substrates with a residual moisture of up to 6 % by weight and a substrate temperature ≥ 2+ °C can be plastered. Plaster base is used with ceiling temperature control systems with plaster thickness›s from 20 to 25 mm.
Mixing pump G4 / G5
■ Stator D3-6
■ Rotor D3-6
■ Mortar hoses Ø 25 mm
■ Wet mortar pumping distance up to 30 m
Manual application
Mix the contents of one bag with approx. 19 litres of clean water without further additions using an agitator until an application-ready
consistence is achieved.
Machine application
Adjust the water feed to achieve a lean mortar consistence (approx. 1 bar /metre mortar hose). Depending on the temperature, breaks in spraying not exceeding 10 to 15 minutes are possible. Clean the machine and hoses with longer breaks / interruptions in application.
Application
In order to create a level surface, spread the thrown-on / applied or machineapplied material flush and perpendicular with a H-straight edge. After initial setting has commenced, level with a feather edge and align the corners. If required, the surface can be re-worked with a wide spatula. After wetting the plaster surface with a sponge float, create enough plaster sludge and smoothen and sponge minor unevenness. After the plaster surface has set lightly, smoothen it with a wide spatula or finishing trowel. On non-frictionally bonded components between the wall and ceiling, reveal connections, etc. the separation must be continued with a separation (trowel) cut in the plaster layer. Separating strip is recommended instead of a separation cut.
Provide good ventilation to ensure quick drying of the plaster. The drying time at 10 mm plaster thickness is an average of 14 days depending on the humidity, temperature and ventilation of the room. The drying time will be extended with unsuitable temperatures / air humidity. If mastic asphalt screed is applied after plastering, sufficient transverse ventilation is required to avoid thermal stresses.
Single- or double-layer: 8 to 50 mm
Single-layer 8 to 50 mm
Average plaster thickness 10 mm, minimum plaster thickness 8 mm. Cover tape conduits by min. 5 mm. In special cases, a plaster thickness of up to 50 mm can be applied in a single-layer to a wall, however, application of 2 layers should be considered when the plaster thickness exceeds 35 mm, as there is an increased drying time before further coatings can be applied with a single-layer. The overall drying time is reduced when the first plaster layer dries more quickly.
Double-layer ≥ 35 to 50 mm
Roughen the first layer with a trapezoid metal sheet or similar and apply suitable primer when fully dry. The next layer can be applied after the first layer is fully dry.
(Concrete) Ceilings may only be plastered as a single-layer and a maximum plaster layer of 15 mm.
EPS boards and sheathing blocks as well as wood wool lightweight boards should have a single-layer applied and the entire surface must be reinforced (see reinforcement). Minimum plaster thickness 15 mm.
Application as a single-layer in a minimum plaster thickness of 10 mm. Level and roughen wall surfaces after application. Do not smoothen or sponge the surface. Allow to dry and set fully before priming and applying a tile covering. In non-commercial bathrooms and kitchens (e.g. WCs in schools, bathrooms in hotels, hospitals, residential-care and nursing homes) as substrates for tiles and floor slabs, if the weight of the tiles and floor slabs including the thin-bed mortar does not exceed 25 kg/m².
With a material change in the plaster substrate, with insulation boards,etc., bed reinforcement mesh in the upper third of the plaster layer with at least 100 mm joint overlap and 200 mm overlap on all sides to the flanking component. The plaster is applied wet-in-wet in two layers, whereby the first layer has not yet started to set on the surface when the 2nd layer is applied.
Up to about 180 minutes depending on the plaster substrate.
Do not apply material at air and/or substrate temperatures below +5 °C and above +30 °C.
Clean the machines and tools with water immediately after use.
Fire protection enhancement
Without plaster base (up to 15 mm plaster thickness)
A 10 mm thick plaster layer is equivalent to 10 mm of normal concrete used for the concrete cover of the reinforcement. Pretreatment with rough cast is necessary.
With non-combustible plaster base
A non-combustible plaster base is required for plaster thickness´s
≥15 mm to 25 mm. Here 8 mm thick plaster with a plaster base is equivalent to 10 mm of normal concrete. The maximum plaster thickness on the plaster base is 25 mm. The plaster must penetrate the coarse meshed plaster base by ≥10 mm and with ribbed expanded metal by ≥5 mm.
Product description
Coatings
The plaster must be dry, free of loose bits and dust-free for all coatings and linings. Apply primer to suit the subsequent paints/coatings/linings, generally
a deep primer. Apply a wallpaper paste layer to the wall for wallpapers.
Technical specifications
The stated technical data were evaluated acc. to the respective test standards. Deviations under site conditions are possible.
Material requirement and efficiency
The exact consumption can only be determined with a test application on the individual object.